Process Safety and
Disaster Prevention/BCP
At the Nippon Soda Group, recognizing that the continuation of safe, stable production activities and the stable supply of products and services is fundamental to our business activities, we promote process safety and disaster prevention activities. Further, we are constantly working to improve our business continuity plan so that we can quickly recover and restart production activities in the event of a natural disaster or other emergency, and at the same time reinforcing our stable supply structure.
- Regular inspections, repair and renewal of equipment and training of operators at each manufacturing site.
- Improvement of the risk management system through emergency drills and education to prepare employees for possible accidents and disasters.
- Safety reviews by our internal experts to verify safety when facilities are constructed or renovated. Regular diagnoses of our disaster prevention capabilities by external specialists.
- Regular reviews and improvement of our business continuity plan (BCP), which is designed to ensure preparedness for natural disasters such as large-scale earthquakes and other emergencies that could result in extensive damage.
Process Safety and
Disaster Prevention
Risk Management
Risk assessment of process safety and disaster prevention |
We conduct risk assessments related to safety and disaster prevention for facilities, machines and manufacturing processes. Identified risks are prioritized and, accordingly, measures to ensure the safety of facilities are implemented and inspections are conducted in sequence. |
---|---|
Establishment of an emergency risk management system | We give the highest priority to preventing accidents and disasters. On the other hand, to prepare for unavoidable accidents and disasters, we have established an emergency risk management system and conduct periodic drills and exercises to maintain the system in a sound condition. |
Standards on Emergency Response |
The Standards on Emergency Response have been developed to ensure prompt and appropriate communication, response, and instruction in the event of a disaster or accident, and their effectiveness is reviewed and revised periodically, and confirmed through training. |
Third-party diagnoses of disaster prevention capabilities
Sompo Risk Management Inc. regularly diagnoses the disaster prevention capabilities of Nippon Soda and its manufacturing Group companies. (Diagnoses were cancelled in FY 2022 to prevent the spread of COVID-19)
Safety Management
Safety audit to confirm the safety of plants
To ensure the safety of processes in the construction and renovation of facilities, the Nippon Soda Group undergoes safety reviews and audits by managers and internal experts. Facilities and operations are inspected for safety, work environment, quality and other factors.
Facilities of Group manufacturing companies undergo periodic RC audits to assess the management conditions of manufacturing facilities, and the results are incorporated into activities to improve process safety and disaster prevention.
Safety audits prior to trial operation by the Head Office
Chiba Plant, July 7, 2021
Safety audits prior to trial operation of pilot testing/manufacturing facility for samples of new specialty polymer SBS.
As a result of document and on-site audits, 32 safety issues were identified. After implementing countermeasures for all of these safety issues, trial operation was complete.
Education and Drills for Disaster Prevention
Nippon Soda provides a variety of process safety and disaster prevention training for employees to acquire the knowledge and skills to ensure their safety. We will continue to promote safety and disaster prevention activities with the aim of further improving our safety and disaster prevention activities to achieve the target of “no major accidents at facilities.”
Group training
Each worksite and department conducts continuous education and training in accordance with the CSR action plan. Further, for new employees assigned to our manufacturing sites, we provide manufacturing training programs as a form of new employee training. These programs include experiential education and training related to safety and basic work practices.
In FY 2022, the programs were implemented on a limited basis while adjusting times and numbers of participants to prevent the spread of COVID-19.
- July 19–29, 2021: Takaoka Plant (practice) No. of participants: 17
- August 18–24, 2021 (temporarily cancelled due to number of infections)
October 4–10, 2021: Takaoka Plant (first-year training) No. of participants: 6 - October 19–28, 2021: Takaoka Plant (second-year training) No. of participants: 5
- November 15–19, 2021: Nihongi Plant (first-year training) No. of participants: 6
- December 6–10, 2021: Nihongi Plant (second-year training [1]) No. of participants: 4
- December 13–17, 2021: Nihongi Plant (second-year training [2]) No. of participants: 5
Disaster prevention system working in cooperation with local communities
Each Nippon Soda site implements regular disaster drills, which include drills conducted in cooperation with other nearby plants and local governments. These drills are conducted taking into account the environment and other characteristics unique to each region so that they can be applied in real settings.
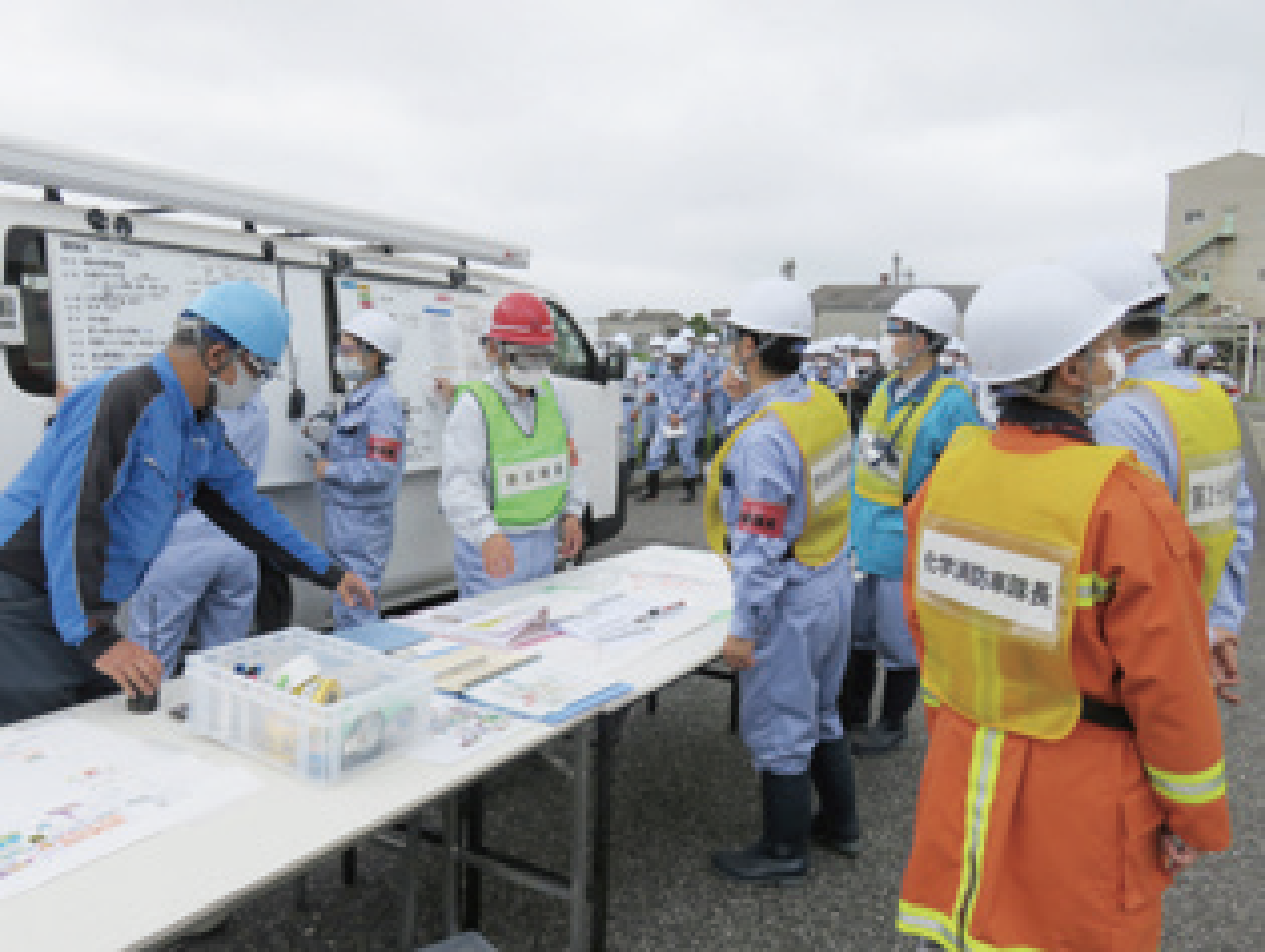
Comprehensive disaster drill
(Chiba Plant/Chiba Research Center, May 21, 2021)
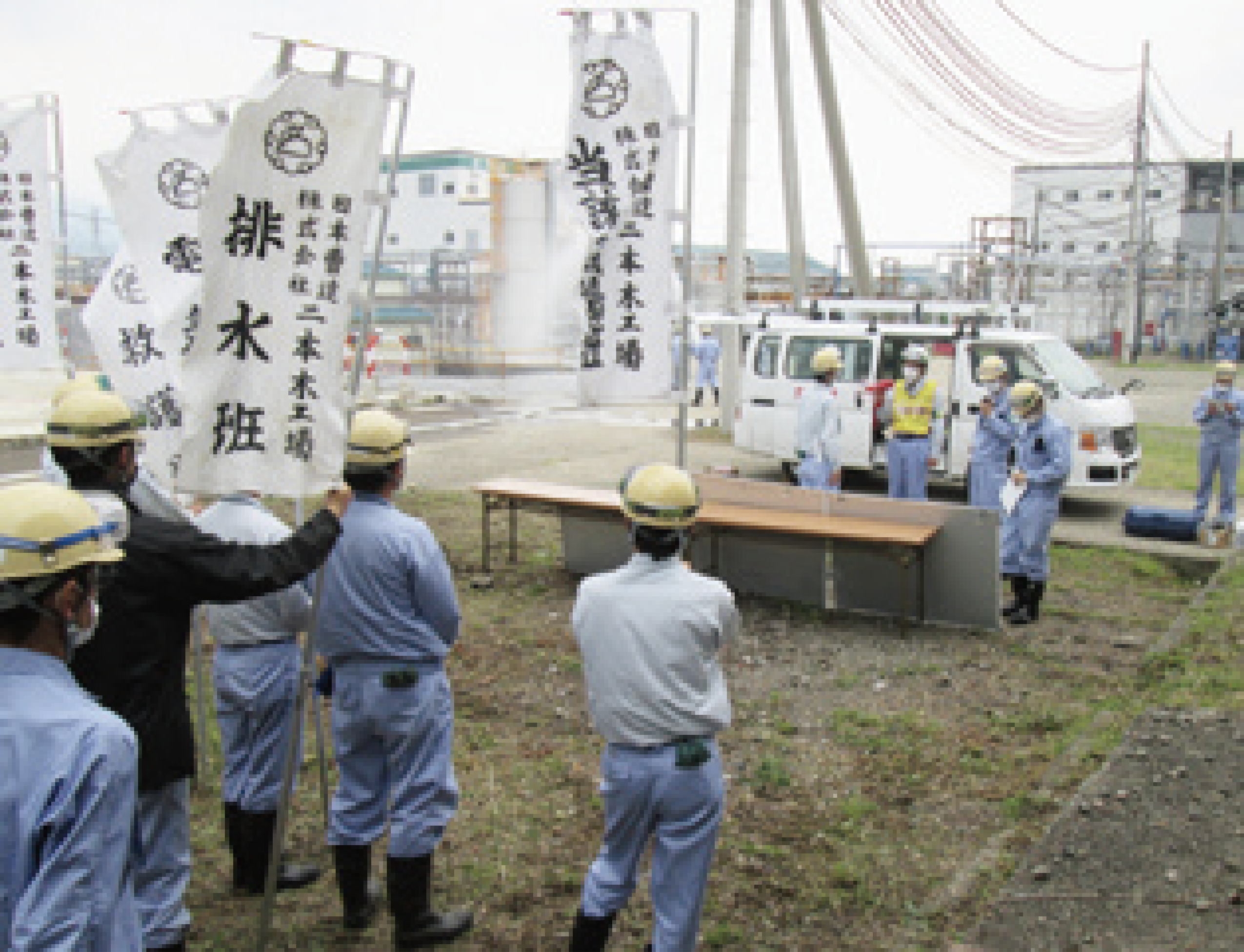
Spring disaster drill
(Nihongi Plant, June 22, 2021)
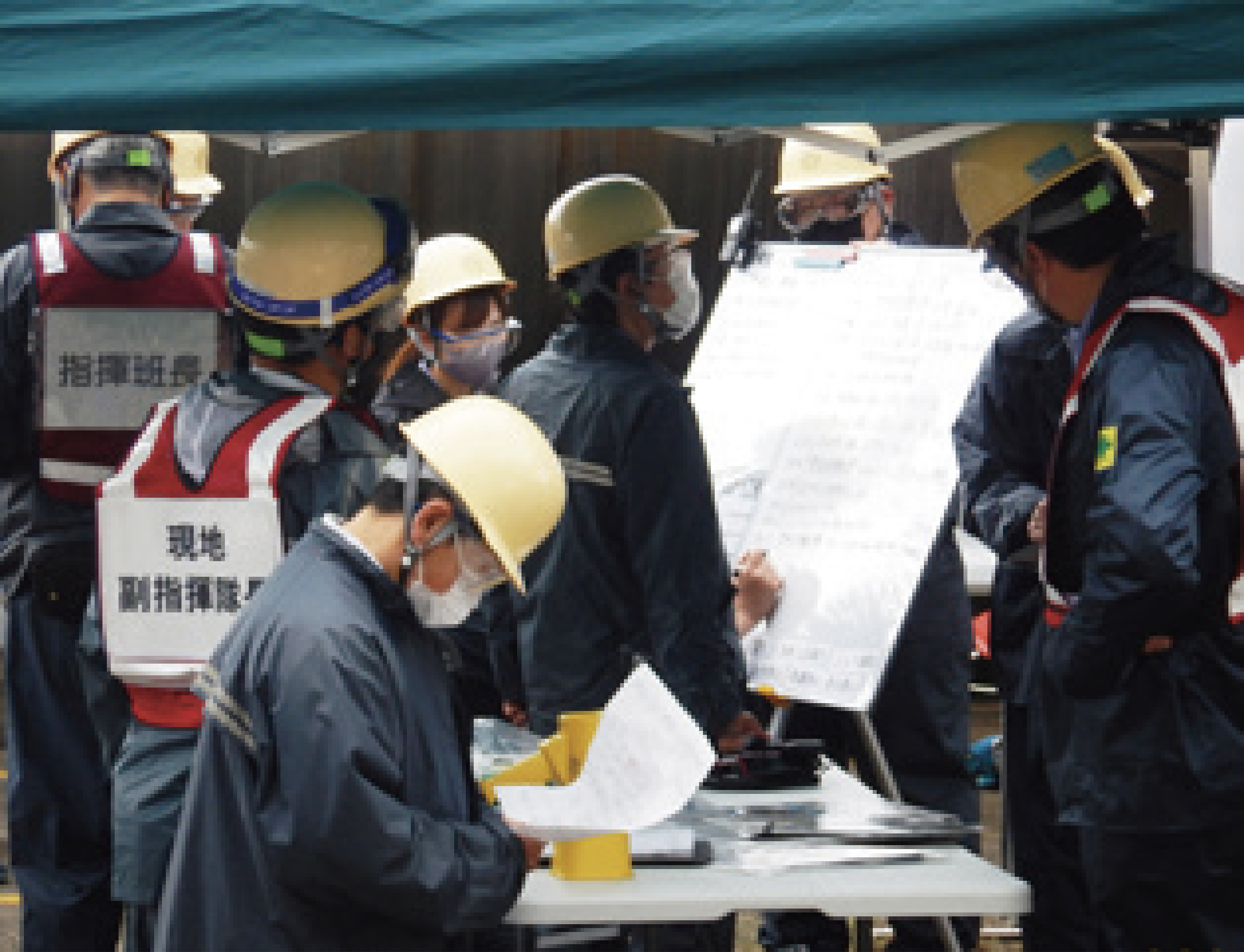
Environmental abnormality response drill
(Takaoka Plant, October 13, 2021)
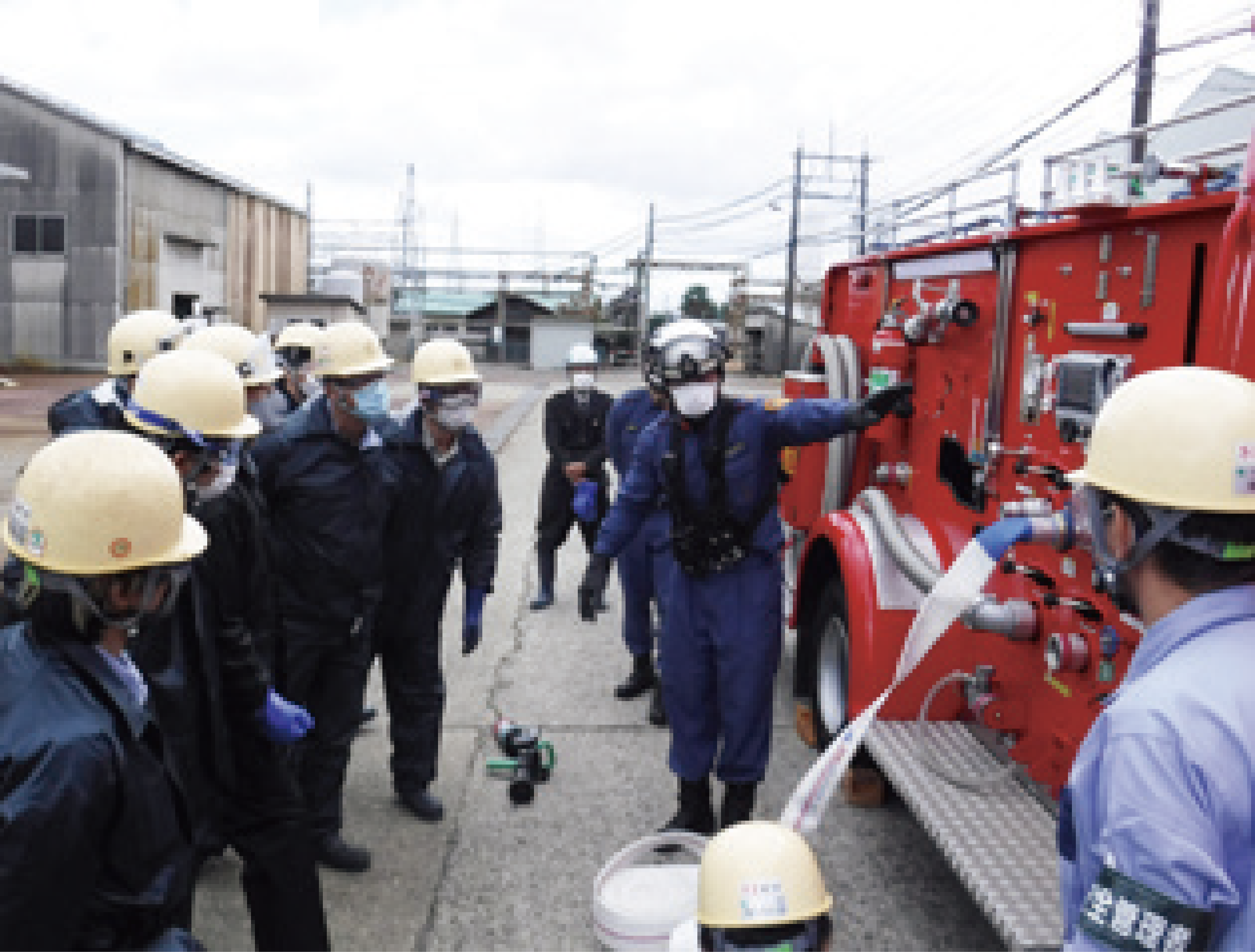
Education on firefighting techniques by the Takaoka Fire Department
(Takaoka Plant, October 29, 2021)
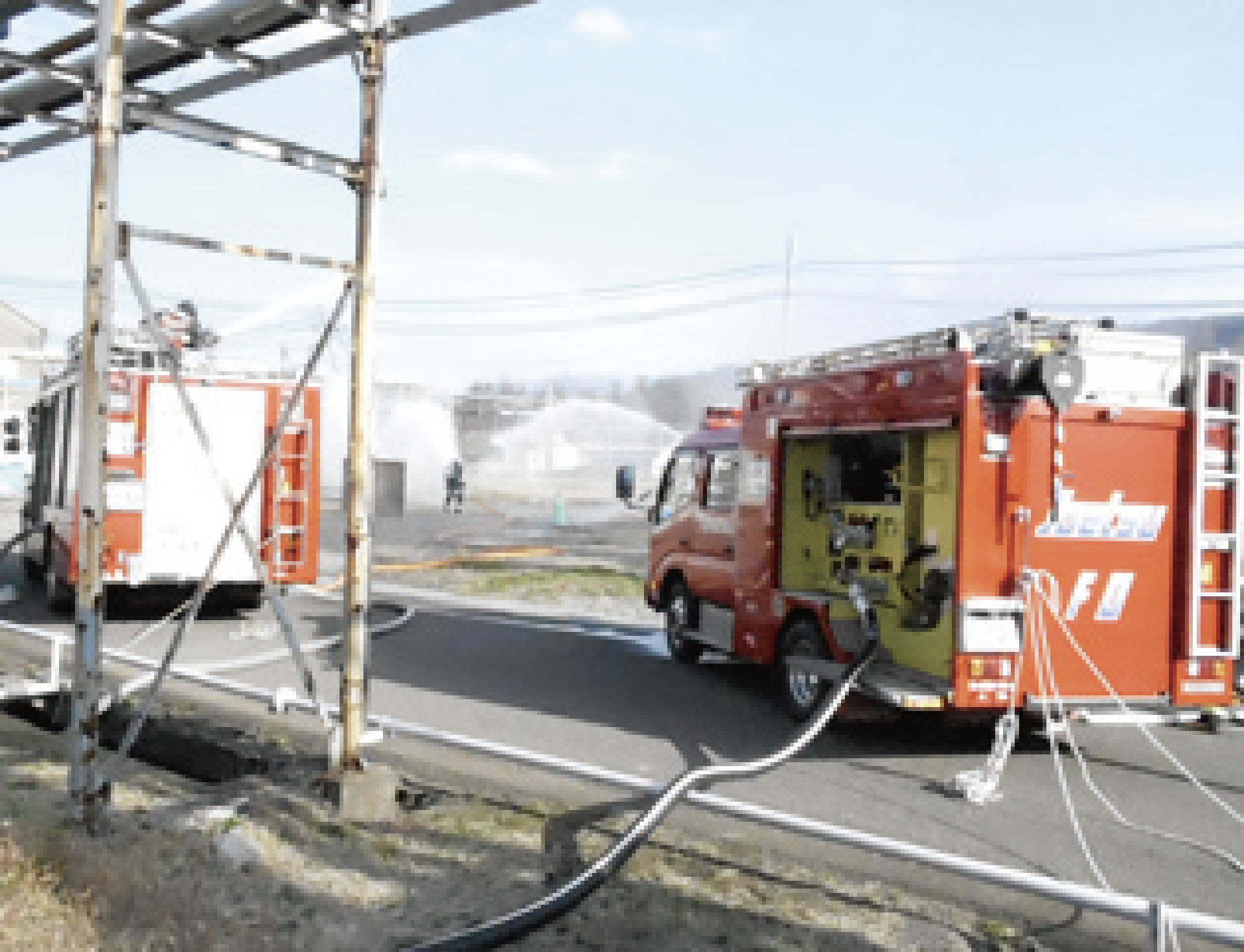
Autumn disaster drill
(Nihongi Plant, November 19, 2021)
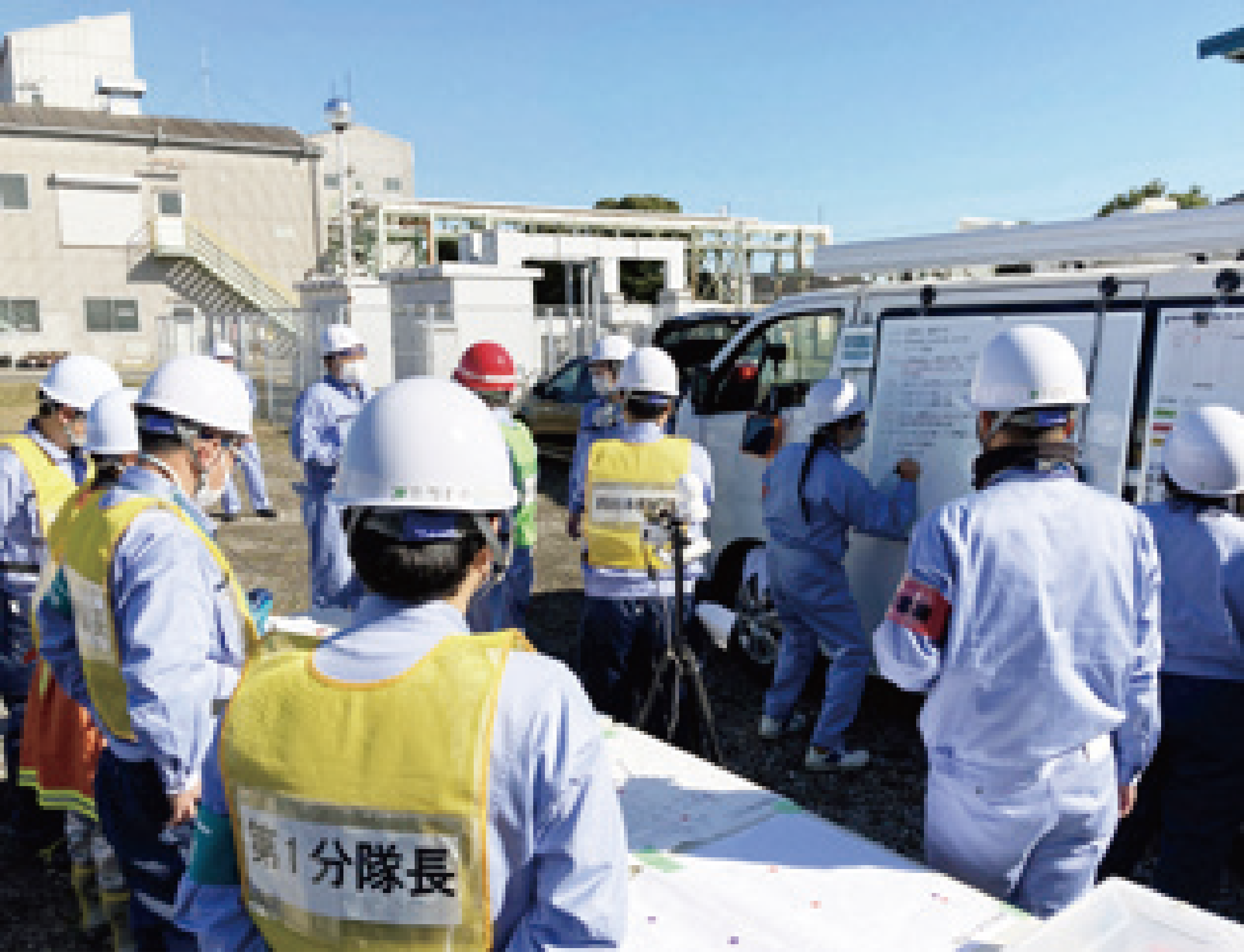
Comprehensive disaster drill
(Chiba Plant/Chiba Research Center, November 25, 2021)
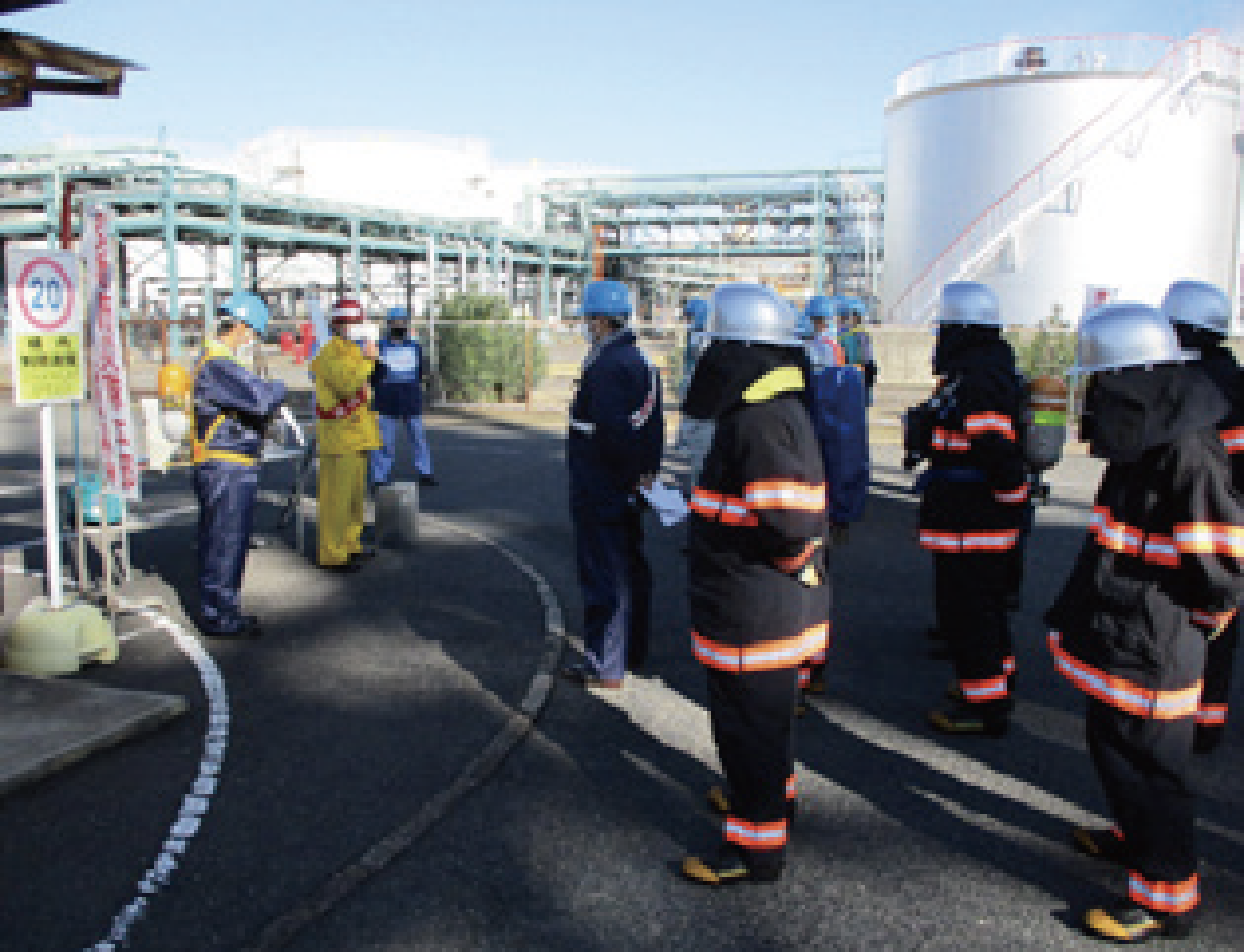
Joint in-plant disaster drill
(Mizushima Plant, December 2, 2021)
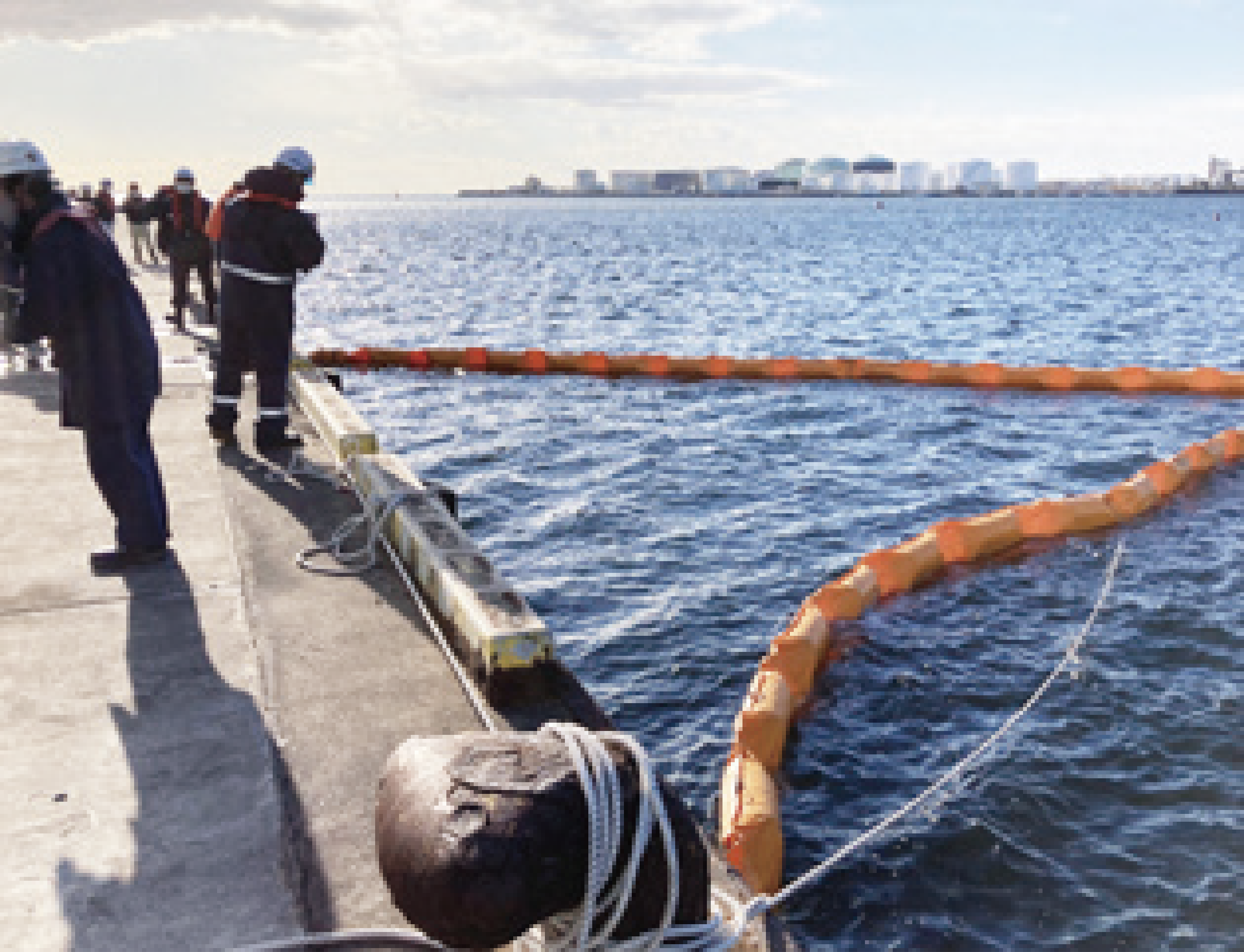
Joint Marine Disaster Management Council emergency report drill
(Chiba Plant, January 14, 2022)

Hazardous material (HCN) leak response drill
(Mizushima Plant, February 16, 2022)
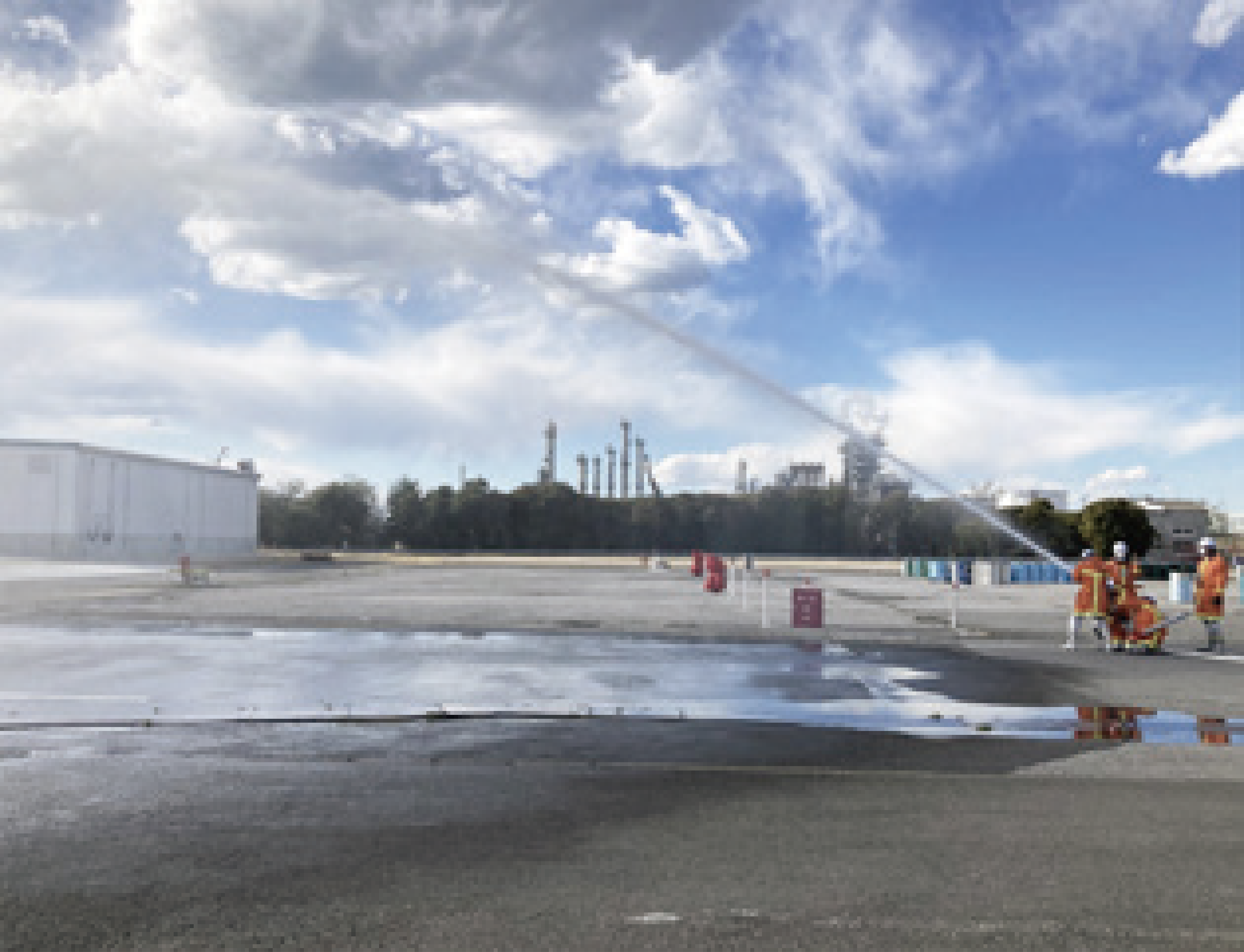
Comprehensive disaster drill
(Chiba Plant/Chiba Research Center, February 17, 2022)
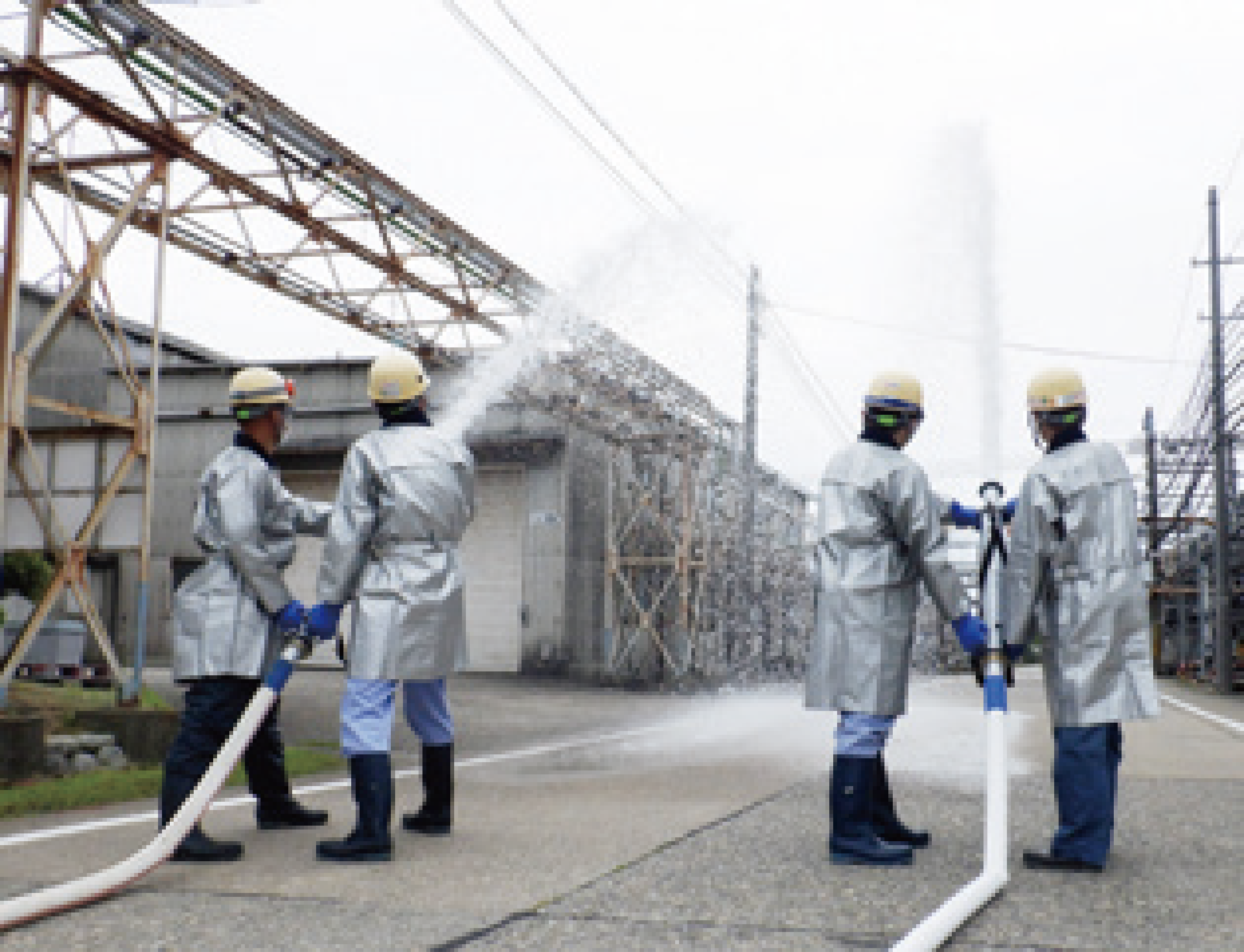
Comprehensive plant disaster drill
(Takaoka Plant, June 8, 2022)
Emergency Drills (FY 2022)
First half (dates of drills) | Second half (dates of drills) | |||
---|---|---|---|---|
Date | Details | Date | Details | |
Nihongi Plant | June 22, 2021 | Spring plant disaster drill | November 19, 2021 | Autumn disaster drill |
Takaoka Plant | April 22, 2021 | Emergency contact drill (using Otsutae-kun) | October 13, 2021 | Environmental abnormality response drill |
June 8, 2021 | Comprehensive spring plant disaster drill | October 18, 2021 | Emergency contact drill (using Otsutae-kun) | |
August 24-27, 2021 | Nighttime emergency report drill (Organic Sec. 2, Formulation Sec.) | October 19-26, 2021 | Fire drill | |
Monthly | 119 report and contact drill | October 22, 2021 | Emergency contact drill to report highpressure gas leaks to regional disaster prevention offices | |
October 26, 2021 | Liquid chlorine tank lorry emergency report drill | |||
October 29, 2021 | Education on firefighting techniques by the Takaoka Fire Department | |||
November 9, 2021 | In-house firefighter training | |||
December 15, 2021 | Emergency contact drill (using Otsutae-kun) | |||
December 22, 2021 | Emergency response drill (for Hokusan Koatsu) | |||
March 9-17, 2022 | Fire drill | |||
March 22, 2022 | Nighttime emergency report drill | |||
Monthly | 119 report and contact drill | |||
Mizushima Plant | May 16, 2021 | Emergency contact drill (using Otsutae-kun) | October 13, 2021 | Response drill for accidents during product transportation (paper-based drill) |
July 16, 2021 | Emergency contact drill (using Otsutae-kun) | November 16, 2021 | Emergency contact drill (using Otsutae-kun) | |
July 16, 2021 | Actual power outage drill | December 2, 2021 | Joint in-plant disaster/evacuation drill | |
July 27, 2021 | Harmful substance (NaOH) leak response drill | January 16, 2022 | Emergency contact drill (using Otsutae-kun) | |
September 16, 2021 | Emergency contact drill (using Otsutae-kun) | February 16, 2022 | Harmful substance (HCN) leak response drill | |
March 16, 2022 | Emergency contact drill (using Otsutae-kun) | |||
Chiba Plant | April 26, 2021 | Emergency contact drill (using Otsutae-kun) | October 12, 2021 | Report drill (Minami-Kinoene) |
May 21, 2021 | Comprehensive joint plant disaster drill for predicted worksite disasters | October 13, 2021 | Emergency contact drill (using Otsutae-kun) | |
August 3, 2021 | Emergency contact drill (using Otsutae-kun) | October 25, 2021 | Ichihara City public disaster drill (cancelled) | |
August 24, 2021 | Petroleum complex risk prediction and response drill | November 12, 2021 | Environmental abnormality response drill | |
August 26, 2021 | Disaster drill for predicted nighttime and holiday emergencies | November 25, 2021 | Comprehensive joint plant disaster drill for predicted worksite disasters | |
January 14, 2022 | Joint Marine Disaster Management Council emergency report drill | |||
February 17, 2022 | Comprehensive plant disaster drill (joint disaster drill) | |||
March 11, 2022 | Evacuation drill (for predicted leakage of harmful gases at other companies) | |||
Odawara Research Center | November 4, 2021 | Disaster drill (Bandai) | ||
November 5, 2021 | Safety confirmation response drill | |||
November 5, 2021 | Departmental disaster drill (five departments in Odawara) | |||
November 5, 2021 | Group-based disaster drill (five groups in Haibara) | |||
Chiba Research Center | April 26, 2021 | Emergency report drill | October 13, 2021 | Emergency contact drill (using Otsutae-kun) |
May 21, 2021 | Comprehensive disaster drill | November 21, 2021 | Emergency contact drill (using Otsutae-kun) | |
August 3, 2021 | Emergency report drill | November 25, 2021 | Comprehensive disaster drill | |
August 26, 2021 | Disaster drill for predicted nighttime disasters | February 17, 2022 | Comprehensive disaster drill | |
September 2021 | Emergency evacuation drill (desk-based training) | March 2022 | Emergency evacuation drill (desk-based training) | |
Head Office | December 2021 | Comprehensive disaster drill at the Shin-Otemachi Building (cancelled) | ||
January 25, 2022 | Safety confirmation report drill |
Accident Report
Anhydrous sulfuric acid leakage at delivery destination, Chiba Sales Office, Sanso Unyu Co., Ltd.
- 1.Date/time of accident:July 19, 2021; around 9:00 am
- 2.Accident overview
Due to partial damage to the tank of a tank lorry carrying anhydrous sulfuric acid—which is manufactured and sold by Nisso Metallochemical Co., Ltd., and transported by Sanso Unyu Co., Ltd., the transportation department of Sanwa Soko Co., Ltd.—the product leaked on the customer’s factory premises, generating a mist and abnormal odor. There were no personnel casualties or injuries, nor was there any negative impact to the environment outside the premises. - 3.Cause
Partial damage to the tank of the tank lorry caused by age-related corrosion. - 4.Recurrence prevention measures
- ①Manufacture of new tanks
We reviewed tank materials and created a new tank that is resistant to corrosion. - ②Implementation of risk assessments
We will implement risk assessments to reduce the risk of leakage in every process from the shipment of anhydrous sulfuric acid to delivery. - ③Review of tank inspection methods
We have reviewed and strengthened our inspection methods for both our existing tanks and new tanks. (Inspection of tank thickness [annually], installation of inspection openings in the relevant areas, inspection of tank pressure prior to filling, etc.)
Nisso Metallochemical, Sanwa Soko, and Sanso Unyu will work together to rebuild their emergency support system and create a response manual that anticipates leakage to ensure quick and accurate sharing of information. Further, the three companies will also carry out annual leakage drills to ensure accurate actions and procedures in the event of a leak.
Business Continuity Plan (BCP)
Basic concept of the BCP
In the event of a natural disaster such as a large-scale earthquake or other crisis that can result in serious damage to Company worksites, our social responsibility is to ensure the safety of local residents, full-time and temporary employees and partner company employees. Based on this concept, the principles of the BCP are defined as follows:
- 1.The highest priority is placed on checking the status and ensuring the safety of Nippon Soda’s own employees, partner company employees and temporary employees and their families, and ensuring the safety of residents in communities where the Company’s business sites are located.
- 2.The consciousness of serving the public and community is shared among all personnel throughout the Company.
- 3.Efforts are focused on protecting the safety of the affected Head Office, plants, research centers, branch offices and sales offices.
- 4.Measures should be taken to establish a system that allows Nippon Soda’s employees, partner company employees and temporary employees who are engaged in ensuring safety and security to act flexibly and at their discretion according to the circumstances.
Continuation of supply of products according to customer needs
The BCP of Nippon Soda aims to ensure, in the event of a natural disaster or other crisis, safety as well as the supply of products to customers as requested. To achieve this objective, improvement is accelerated using the PDCA cycle.
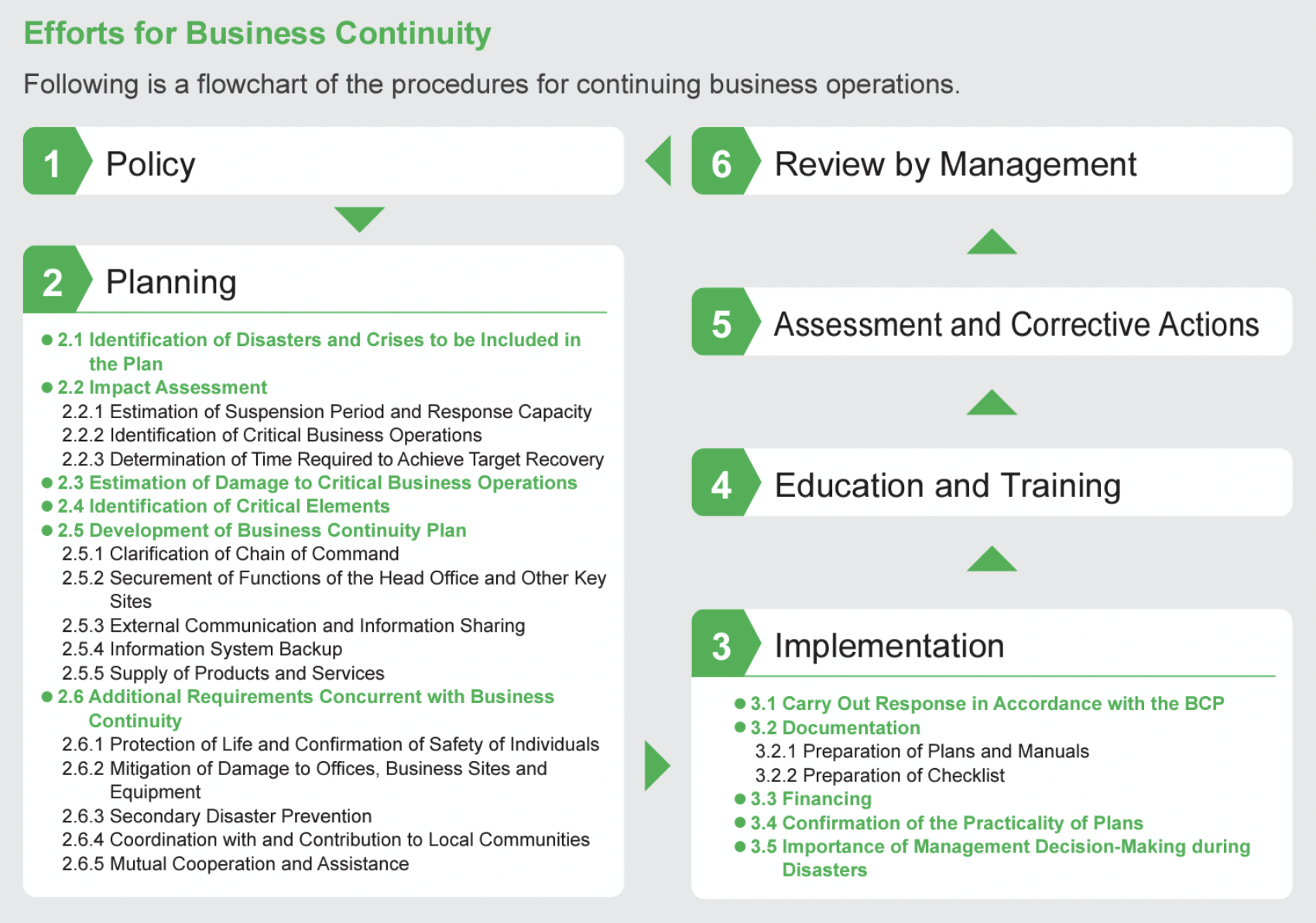
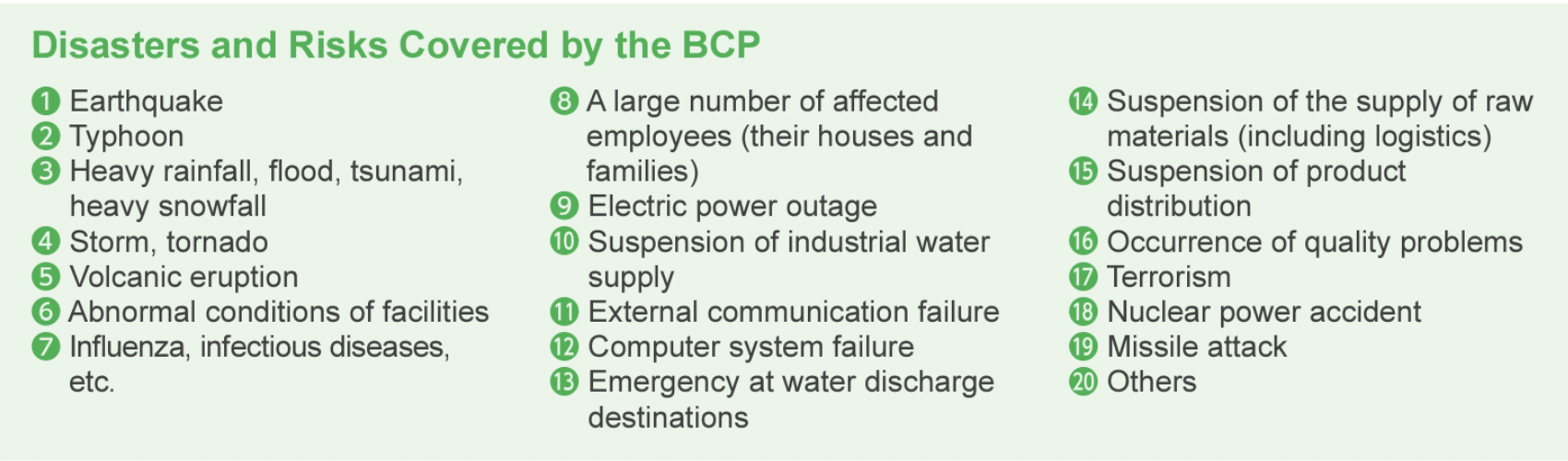
(Achievement levels ◎:≥ 90% ○:80-90% △:60-80% ╳:≤ 60%)
1. Major accidents at facilities: Target: Zero accidents | Achievement level ╳: One major facility accident (Group company) One Group company (Isohara Plant Unit 1, Nisso Fine: Damage to waste gas combustion furnace blower) |
---|---|
2. Maintenance and improvement of the BCP | Achievement level ◎: The 11th version was distributed and the 12th version was prepared. |
We will continue our efforts to achieve the target of “no major accidents at facilities” through the constant improvement of safety management, risk management, education, disaster prevention drills and other measures. We will also improve and review the BCP in a systematic manner.